Research Highlight 8 – Polyesters Directly Produced from Biomass for a Circular Economy
- Sini Nalakathu Kolanadiyil
- Jul 18, 2022
- 13 min read
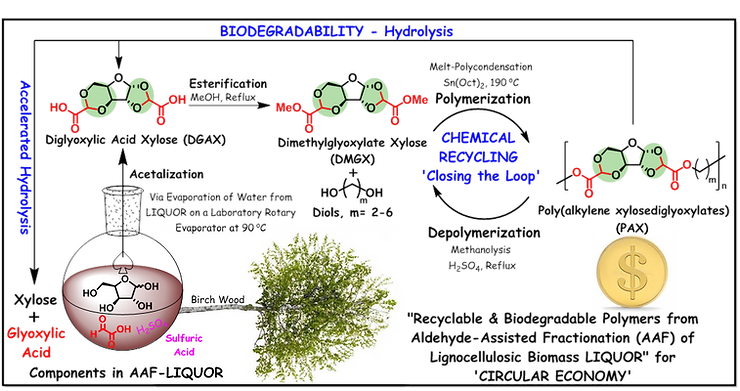
To deal with current plastic pollution and our material dependency on finite resources, a shift from current linear economy (take–make–use–dispose) to a circular economy (take–make–use–recycle) has now become necessary and unavoidable [1]. Lignocellulosic biomass is one of the most abundant renewable resources available on the earth, that can be utilized for this purpose – for designing of novel recyclable polymers. However, the research in this field is majorly focused on exploiting either cellulosic components (cellulose and hemicellulose) for producing high quality cellulose for pulp and paper industry, carbohydrates for second generation bioethanol and platform chemical production {5-hydroxymethylfurfural (5-HMF), furfural – and it’s further upgrading}, which results in a highly condensed lignin due to the harsh conditions employed during fractionation, and thus it’s use is limited for producing energy [2-4]. Otherwise, the research is devoted in the direction of fractionation of high quality lignin under mild conditions to avoid condensation reaction and improve the yield of aromatics that can be further utilized for the production of drop-in-chemicals or as a polymer building block with further upgrading process [4]. Here, Prof. Jeremy S. Luterbacher and colleagues at École Polytechnique Fédérale de Lausanne (EPFL), Switzerland, came up with a plot twist in the story with their strategy “Aldehyde Assisted Fractionation (AAF) of Lignocellulosic Biomass” to produce recyclable and degradable biopolymers – polyesters named poly(alkylene xylosediglyoxylates) (PAX). The work is recently published in “Nature Chemistry” (see Main Figure) [5].
In their AAF strategy, the utilization of an aldehyde with a secondary functionality such as ‘glyoxylic acid’ allowed efficient fractionation of all major three components from the lignocellulosic biomass (birch wood) in the presence of an acid catalyst {such as sulfuric acid (H2SO4) or hydrochloric acid (HCl) – a simple filtration of the reaction mixture to obtain cellulose rich solids and followed by precipitation of the concentrated solution by addition of water to obtain glyoxylic acid stabilized lignin. The remaining liquor – consisting of xylose produced via depolymerization of hemicellulose (xylan), unreacted glyoxylic acid and the acid catalyst employed – is utilized to produce a novel monomer ‘Dimethylglyoxylate Xylose’ (DMGX) that can provide degradability/recyclability in the polymer (see Figure 1). This process involves a simple evaporation of water from the AAF lignocellulosic liquor on a laboratory evaporator (at 45-90 °C), which allows acetalization of xylose with glyoxylic acid and forms a diacid monomer ‘Diglyoxylic Acid Xylose’ (DGAX) and subsequent esterification of carboxylic acid functionality in DGAX in methanol resulted in DMGX. Polyesters (that is PAXs) are produced via melt-polycondensation (at 190-200 °C) of DMGX with various aliphatic diols in the presence of a Lewis acid catalyst, for example, poly(pentylene xylosediglyoxylate) (PPTX) is produced by reaction of DMGX with 1,5-pentanediol. PAXs are the first sugar-based polyesters directly produced from lignocellulosic biomass by taking advantage of its fractionation method! Currently, 2,5-furandicarboxylic acid (FDCA) monomer is used to produce bio-based polyester such as poly(ethylene furanoate) (PEF) as an alternative for petro-based poly(ethylene terephthalate) (PET). However, FDCA production from lignocellulosic biomass involves many steps – enzymatic hydrolysis of cellulose into glucose, isomerization of glucose to fructose, then dehydration of fructose to produce platform chemical 5-HMF, and finally catalytic oxidation of 5-HMF to FDCA [6]. Thus, DMGX produced from AAF liquor has the potential to replace both FDCA and petro-based monomer terephthalic acid (TPA) in industrial PET production, in terms of its simplified process and renewability.
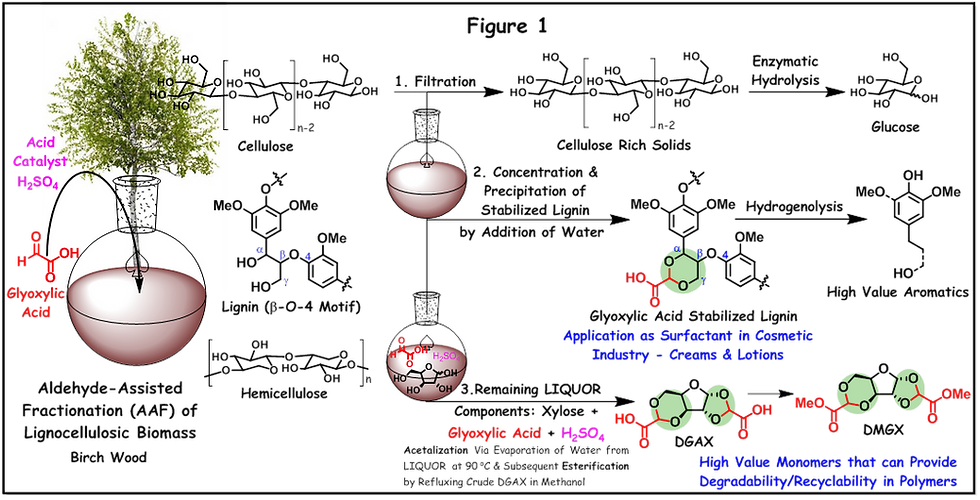
Prof. Luterbacher has introduced this AAF strategy in 2016 with the aim of protecting benzylic alcohols (α-OH) on the lignin backbone (see Figure 1, lignin β-O-4 motif) from undergoing dehydration during fractionation – which forms reactive benzylic carbocation – that can undergo electrophilic substitution reaction with aromatic rings on the lignin to form C-C bonds [7]. This generally results in poor quality condensed lignin with low β-O-4 content and thereby a low yield for aromatic monomers after depolymerization. His AAF strategy, that is, protection of α,γ-OH diols with aldehyde such as formaldehyde or propionaldehyde stabilized lignin during lignocellulosic fractionation via acetal formation (1,3-dioxane type, see Figure 1) – which resulted in a near theoretical yield of aromatic monomers after hydrogenolysis {mainly 4-propanolguaiacol/syringol & 4-ethylguaiacol/syringol} [7,8]. This study also revealed in situ acetal protection of C5/C6-sugars produced from hydrolysis of cellulose/hemicellulose during fractionation – for example formation of diformylxylose via in situ acetalization reaction of formaldehyde with diols in xylose – which prevented these sugars from undergoing dehydration. Prof. Luterbacher has now able to practically utilize those previous research insights for making recyclable and degradable polymers that have the real potential to mitigate ‘plastic pollution’. In order to proceed in situ acetal protection, water content in the fractionation medium should be minimal [9] and a secondary functionality in glyoxylic acid reduced it’s reactivity as compared to formaldehyde – thus, xylose remained unreactive during fractionation in the presence of glyoxylic acid. This also simplified the isolation of the other two components (cellulose rich solids and glyoxylic acid stabilized lignin), at the same time provided an easy accessible liquor, which can be directly used for DMGX production without the need for any additional reagents! In the article, further enzymatic hydrolysis of cellulose to produce glucose is demonstrated. Also, hydrogenolysis of glyoxylic acid stabilized lignin to produce high value aromatics (see Figure 1). The glyoxylic acid stabilized lignin can also be utilized as it is – without any further modification/depolymerization/upgrading. In a separate study [10], Prof. Luterbacher and his team have demonstrated it’s application as a surfactant in cosmetic industry (hand creams and lotions). Thus, the whole strategy is highly profitable. This is a perfect example of an ideal biorefinery where all components of lignocellulosic biomass are utilized for high-value applications.
Very few reports are available on a complete biomass utilization [11,12]. Examples are: (1) fractionation of lignocellulosic biomass using γ-valerolactone/water and sulfuric acid – in which high purity cellulose pulp was extracted for textile fiber production, hemicellulose fraction was utilized to produce platform chemical ‘furfural’ and lignin fraction was utilized to produce high value carbon based products (carbon foam) [11]; and (2) Reductive catalytic fractionation (that is, lignin-first approach) of lignocellulosic biomass in the presence of a metal catalyst (Ru/C) and hydrogen – which produces two fractions – a carbohydrate pulp and a lignin depolymerized oil (monomer & oligomers) {via solvolysis–hydrogenation–hydrogenolysis processes}. The carbohydrate pulp was utilized for bioethanol production (via semi-simultaneous saccharification-fermentation), monomer fraction from the lignin oil was utillized for producing drop-in chemicals ‘phenol and propylene’ (via catalytic funneling – hydroprocessing + dealkylation) and oligomers for replacing fossil-based ‘para-nonylphenol’ in lithographic printing ink [12]. Prof. Luterbacher’s strategy is simple and stands out from these works because it focuses on the direct development of circular polymers from lignocellulosic biomass.
Large scale synthesis of DMGX using commercial xylose is also demonstrated in the article by reacting with glyoxylic acid in the presence of sulfuric acid using a one-pot and two-stage acetalization + esterification (in methanol) process. DMGX obtained from both AAF lignocellulosic liquor and commercial xylose are structurally identical and consists of a mixture of 4-stereoisomers – obtained as a transparent oil after distillation from the crude mixture at 180 °C, followed by activated carbon treatment (to remove yellow impurities). The Luterbacher team also has a more simplified process for DMGX purification (instead of neutralization–extraction–distillation steps) by precipitation of crude mixture in ice, which yielded slight yellowish white powder (62%). Currently, they are exploring a different antisolvent that could enhace the yield of the precipitate and also allow the direct recycling of other components in the crude reaction mixture: glyoxylic acid, sulfuric acid and methanol. DMGX oil can also be crystallized, either as crystals of 4-stereoisomers by dissolving in hot ethanol (77%; crystallization at -20 °C) or these 4-stereoisomers can be resolved by crystallization using cyclopentyl methyl ether as 34% of a single isomer (crystallization at 4 °C) and 38% of 1:1 mixtures of two isomers (crystallization at -20 °C). The oil (4-stereoisomers) is used for most of the PAXs synthesis, by reacting with diols of different aliphatic chain length (m= 2-6, see Main Figure), except in case of PPTX and PHX – in which a single isomer of DMGX (obtained via AAF lignocellulosic liquor) was also reacted with 1,5-pentanediol/1,6-hexanediol for structure-property correlation. The properties of PAXs produced via AAF liquor and commercial xylose method are same.
The novel polyesters, PAXs are amorphous in nature (including those produced from a single isomer – 1SPAXs) because of the asymmetry in DMGX structure. PAXs {that is, poly(butylene xylosediglyoxylate) (PBX), poly(pentylene xylosediglyoxylate) (PPTX), poly(hexylene xylosediglyoxylate) (PHX) produced from DMGX/1,4-butanediol, DMGX/1,5-pentanediol and DMGX/1,6-hexanediol respectively} exhibited a unique combination of properties such as high glass transition temperature (Tg): 72-100 °C {PEF: ~85 °C; PET: ~75 °C; polylactide (PLA): ~65 °C}, good mechanical properties with tensile moduli (ET) of 2000-2500 MPa, ultimate tensile strength (UTS) of 63-70 MPa, and elongation at break of 50-80% and strong gas barrier properties with oxygen transmission rates (OTR) of 11-24 cc/m2.day.bar (PET: 11.59; PLA: 157) and water vapour transmission rates (WVTR) of 25-36 g/m2.day (PET: 6.2; PLA: 54). These properties are similar to petro-based PET. The tricyclic rigid DMGX structure on the backbone is responsible for these excellent properties.
These PAXs can be easily processed (within the temperature range of 140-200 °C) by using various industrial techniques such as compression moulding, injection moulding, vacuum-forming and twin-screw extrusion + 3D printing. Because of PAXs high plasticity and strain hardening behaviour (especially in PHX), the Luterbacher team believes that PAXs are also suitable for blow moulding process (to produce bottles). They have made various objects (that we use in our day–to–day life) from PAXs by using these techniques to demonstrate their real potential for industrial commercialization and competence with PET and PLA. The Luterbacher team was very grateful to provide some of the pictures of the produced products, see Figure 2 – (a) USB drive packaging using PHX via vacuum forming – in this case, antioxidant such as TPP (triphenyl phosphite) and an optimized catalyst such as tin(II) 2-ethylhexanoate (Sn(Oct)2) {instead of zinc acetate/dibutyltin oxide} were used during melt-polycondensation of DMGX {crystals of 4-stereoisomers produced via ethanol recrystallization} and 1,6-hexanediol in order to prevent colouration in the final product; (b) Cup and EPFL logo made using PBX via twin-screw extrusion and subsequent 3D printing – here, PBX is produced using DMGX oil (4-stereoisomers), which is why yellow colour for the product; (c) Fiber produced using PPTX made from a single isomer of DMGX – in this case no antioxidants were used since no colouration was observed when using a single isomer crystals for the production of thin products {using dibutyltin oxide as catalyst for melt-polycondensation}. These examples thus indicate that PAXs can be mold into any shape using existing industrial infrastructure and plenty of options are available to tailor them (by incorporation of additives) for commercial applications (especially for packaging industry). In their practical utility test, PBX thin cup could withstand boiling water thanks to its high Tg (100 °C) whereas PLA cup became soft and eventually lost its shape.
