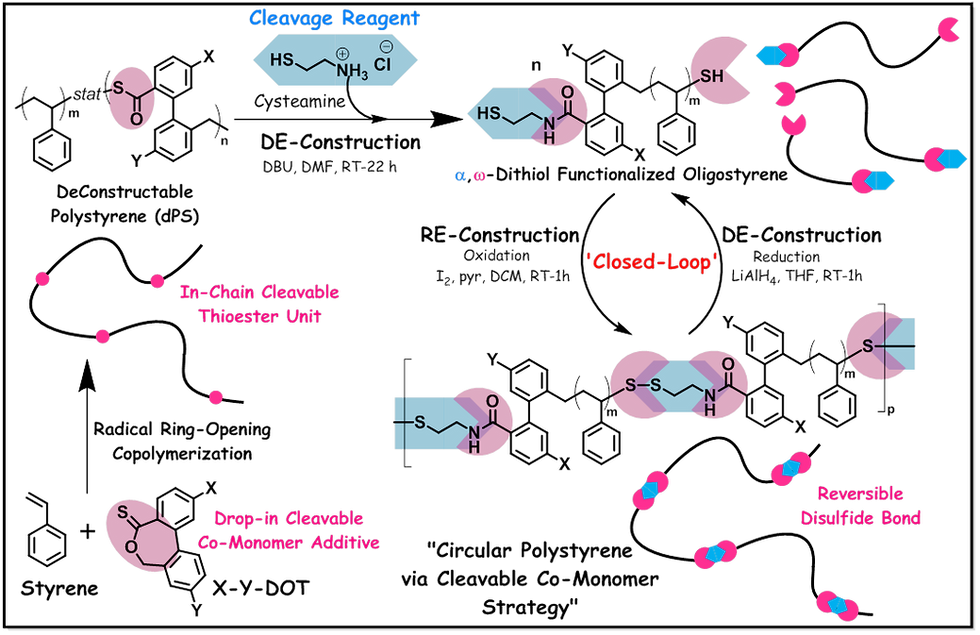
Polystyrene (PS) is a widely used plastic in our daily life – for example in packaging applications (takeaway food boxes, styrofoam cups, disposable cutlery, packaging beads, thermocol boxes), automotive parts, electronics and so on. However, current PS recycling rate is only <1%, which is mainly because it is used in different forms – pure solid, expanded foam (EPS) and as copolymers or blends. The density of the products produced from these varies from 0.016 to 1.04 g/cm3, which makes PS sorting difficult. Also, all PS wastes cannot be recycled together, EPS waste is generally subjected to de-foam prior to mechanical recycling. Otherwise, it is recycled separately via dissolution in a solvent such as limonene and then precipitation into supercritical CO2 to produce foams. Like any other thermoplastics, chain-scission occurs during mechanical recycling of PS, which results in poor quality material and properties [1,2]. The traditional chemical recycling of PS back into its starting monomer 'styrene' requires high energy intensive process to break the C-C backbone. Pyrolysis or thermal cracking is generally employed at high temperature (300-600 °C) in the presence or absence of a catalyst (acid/base), which produces an oil consisting of styrene (~50-70%) and many other aromatic compounds (dimer/trimer of styrene, ethylbenzene, toluene, α-methyl styrene, benzene, indan derivatives and polycyclic aromatic hydrocarbons (PAH)} – isolation of styrene from this oil is almost impossible (very small difference in their boiling points) [3]. The attempt to ‘close-the-loop’ by the direct use of this oil to produce virgin quality PS was not successful as these aromatic compounds were found to act as chain transfer agents during free radical polymerization, which reduced molecular weight and glass transition temperature (Tg) as compared to PS produced from pure styrene monomer. More importantly, the presence of carcinogenic PAH in the recycled PS disqualify it's use in food-packaging applications. Other strategies are focused on upcyling of PS waste, for example, acid-catalyzed aerobic oxidation of PS under visible light to produce high value chemicals such as benzoic acid [4].
To bring circularity in polystyrene, Prof. Jeremiah A. Johnson and his research group at the Massachusetts Institute of Technology (MIT), USA, have ‘re-designed polystyrene' via cleavable comonomer strategy (see Main Figure). The work is very recently published in “Journal of the American Chemical Society” (JACS) [5]. Their invention uses a cleavable comonomer such as thionolactone (X-Y-DOT) at lower loadings (2.5% & 5%) during free-radical polymerization of styrene under bulk conditions (at 130 °C for 15 hours in the absence of an initiator) to produce high molecular weight deconstructable polystyrene (dPS) {Mw: 312 & 258 KDa}. Thionolactone can undergo radical ring-opening polymerization (RROP) {also known as thiocarbonyl addition ring-opening (TARO) polymerization} by addition of a radical onto C=S bond, which induces ring-opening via β-scission of C-O bond leading to a thioester group and a secondary radical that can participate in propagation {see Figure 1 (a)} [6,7]. Thus, copolymerization of styrene with thionolactone (X-Y-DOT) resulted in ‘in-chain cleavable thioester units' in PS backbone {that is, statistical copolymer of PS and X-Y-DOT, see Main Figure}. These in-chain thioesters can undergo hydrolysis, aminolysis, methanolysis or thiolysis to break the polymer chain into well-defined telechelic oligomeric fragments. Here, the Johnson group has demonstrated successful DE-Construction of dPS by using an additional cleavable reagent such as ‘cysteamine’ which underwent aminolysis with in-chain thioester bonds in PS {in the presence of DBU catalyst in dimethylformamide at room temperature (RT) for 22 hours}, and produced α,ω-dithiol functionalized oligostyrene fragments (thiol-OS) {Mw: 9.1 & 4.5 KDa}. Then, RE-Construction of PS was achieved by taking advantage of α,ω-dithiol functionality in the oligomers – that is, the ability of thiol groups in the oligomeric fragments to undergo oxidative repolymerization to form disulfide bonds {using iodine as oxidant, pyridine as H-I scavenger and dichloromethane as solvent at RT for 1 hour} (see Main Figure). The recycled PS (rPS) obtained in this way has similar molecular weight (Mw: 292 & 287 KDa) as virgin dPS. Note that there is a structural difference here, the virgin dPS does not contain disulfide bonds, instead it possess in-chain thioesters – the Johnson group called this phenomenon “molar mass memory effect” (meaning the ability to remember it’s initial mass after DE-Construction and RE-Construction cycle). Not only that “PS-like thermo-mechanical properties” {which has no cleavable units in the backbone including commercial PS; elastic moduli (E’): 2.55 GPa & Tg: 107 °C} were observed for both virgin dPS {E’: 2.40 GPa & Tg: 107 °C} and recycled PS {E’: 2.61 GPa & Tg: 100-103 °C}. The newly re-designed polystyrene, virgin dPS and recycled PS also exhibited good thermal processing window of 271 °C and 237 °C respectively (PS without cleavable units: 301 °C).
The Johnson group has also demonstrated a second DE-Construction and RE-Construction closed-loop cycle by taking advantage of the reversibility of disulfide bonds in the recycled PS under redox conditions – that is reduction of disulfide bond in rPS {in the presence of lithium aluminum hydride in tetrahydrofuran solvent at RT for 1 hour} to produce oligostyrenes containing dithols – which had identical molecular weight as thiol-OS produced via aminolysis of dPS; and then, thiol oxidation to regenerate PS with disulfide bonds. The recycled PS obtained via this method showed ~55% mass recovery as compared to the virgin dPS (containing in-chain thioesters). The Johnson group has stated in the article that this was achieved with minimal optimization (only catalyst screening), thus improvisation in the procedure can further enhance the recycling efficiency. The highlighted article is the first report showing circularity of PS with near full material property retention. Polystyrene containing disulfide bonds has been reported previously, however by using different strategies – by taking advantage of reversible-deactivation radical polymerization methods (RDRPs). Examples are: (a) Atom transfer radical polymerization (ATRP) of styrene using a difunctional initiator such as dimethyl 2,6-dibromoheptanedioate and CuBr/N,N,N′,N′′,N′′-pentamethyldiethylenetriamine catalyst complex – which resulted in a dibromo terminated polystyrene. The nucleophilic substitution of the bromine end groups in PS with a sulfur precursor such as thiodimethylformamide resulted in PS with thiol end groups, which was then subjected to oxidation to produce PS with disulfide bonds [8]. (b) Reversible addition-fragmentation chain transfer (RAFT) polymerization of styrene using a difunctional RAFT agent such as 1,3-bis(2-(thiobenzylthio)prop-2-yl)benzene (BTBTPB) – which resulted in a PS containing RAFT end groups {PhCH2C(=S)S-}. The aminolysis (using hexylamine) of RAFT end groups led to α,ω-dithiol functionalized PS. Then, oxidation of thiols in PS to form mono-cyclic (under dilute conditions) or linear (under concentrated conditions) PS with disulfide bond(s) [9]. In these studies, the focus was mainly on controlling the structure and molecular weight distribution.
Prof. Johnson’s strategy is very versatile since thionolactone (X-Y-DOT) used herein is a “drop-in additive” and can be copolymerized with any commodity vinyl monomers to produce deconstructable polymers in order to achieve circularity! In this regard, DE-Construction (aminolysis of in-chain thioesters)/RE-Construction (oxidative repolymerization) of polyacrylate (dPA) {that is deconstructable poly(tert-butyl acrylate) produced via RROP of tert-butyl acrylate with DOT} is also demonstrated in the article, and the above-mentioned molar mass memory effect was also found in the recycled PA. Thus, Prof. Johnson believes that this ‘molar mass memory effect’ phenomenon is applicable to other deconstructable vinyl polymers that can be produced via DOT co-monomer strategy – which will enhance their circularity in practical applications (as opposed to current industrial practice of mechanical recycling of thermoplastics – in which polymer undergoes degradation and thereby a decrease in molecular weight was observed).
The use of thionolactone in copolymerization with vinyl monomers has emerged only recently for developing degradable polymers for biomedical applications (drug delivery and tissue engineering) – as an alternative to a widely used cleavable comonomer such as cyclic ketene acetal (CKA) – which undergoes RROP to produce in-chain ester units. However, CKA also undergoes ring-retaining vinylic propagation mechanism during polymerization which introduces non-cleavable acetal rings in the polymer backbone, thereby reducing polymer degradability. Thionolactone is preferred over CKA since such side reaction is not possible because of the reversible reaction of thiocarbonyl moiety with radical species {see Figure 1(a)} [6,7,10-12]. More importantly, in all previous studies the focus was on achieving degradability not on circularity, that is the degraded fragments were never subjected to reformation to produce a polymer (including PS) with virgin-like quality material properties. Prof. Johnson has introduced this concept, for the first-time through this highlighted article – that this cleavable comonomer strategy can be utilized to produce circular vinyl polymers that we encounter in our daily life – such as polystyrene, poly(methyl methacrylate), poly(vinyl chloride), poly(vinyl acetate) and so on – that can eliminate plastic pollution!

The most commonly used thionolactone monomer in the polymer field (to produce degradable polymers) is DOT {that is, dibenzo[c,e]oxepane-5-thione, see Figure 1(b)}. However, previously it has shown no reactivity or low amount of incorporation during copolymerization with styrene, which is mainly because of its low solubility [12]. To enhance DOT's reactivity and solubility in common vinyl monomers, Prof. Johnson has designed new thionolactones containing various substituents at the aromatic rings, X-Y-DOT {see Figure 1(b)}. DOT is generally synthesized via thionation of corresponding lactone, dibenzo[c,e]oxepin-5(7H)-one (DOO) using Lawesson’s reagent. Here, Prof. Johnson’s synthetic strategy varied in DOO precursor synthesis to install the desired substituents on aromatic rings. According to their investigation, the incorporation of fluorine (F) and thioether (SPr) substituents in DOT enhanced it’s reactivity with styrene during copolymerization – with highest reactivity was observed for DOT containing both groups, that is SPr-F-DOT {see Figure 1(b)}. The introduction of SPr group in DOT also showed increased molar solubility in styrene (1:11) as compared to DOT without substituents (1:35), and replacing SPr with a branched alkyl substituent (SBu) resulted in miscibility for all compositions. Using SPr-F-DOT, styrene and divinylbenzene crosslinker (3:100:1 ratio), the Johnson group has also developed deconstructable crosslinked styrenic copolymers. The high reactivity of SPr-F-DOT allowed it’s full incorporation to the crosslinked copolymer structure. DE-Construction of this cross-linked styrenic copolymer was also demonstrated in the article using cysteamine cleavage reagent (aminolysis of in-chain thioesters in the crosslinked copolymer).
