Research Highlight 2 - A Re-Designed Polyethylene with Closed-Loop-Life Cycles.
- Sini Nalakathu Kolanadiyil
- May 31, 2022
- 4 min read
Nearly 360 million tons of plastics are produced per annum, ~50% of them account for packaging applications – that mainly includes polymers such as polyethylene (PE), polypropylene (PP), and polyethylene terephthalate (PET). Most of them are thrown away after a single use application, which then ends up in landfill, oceans and in the open environment. Due to their persistence in the environment, we are facing huge environmental consequences. Recycling of these polymers is necessary for the transition to a circular economy and achieve a sustainable society [1]. Currently mechanical recycling (grinding the product–melting–pelletizing) is widely employed in the industry. However, these polymers are prone to chain scission during reprocessing resulting in poor mechanical properties, hence their reuse is limited to downgrade applications. An attractive strategy is chemical recycling – that is, depolymerization of polymer into its starting monomers and then repolymerization to produce polymer with virgin-quality material properties. However, depolymerization of polyolefins (PE & PP) requires high energy intensive process due to their inert C-C backbone structure and thus difficult to convert it into starting monomers in quantitative yield [2-4].
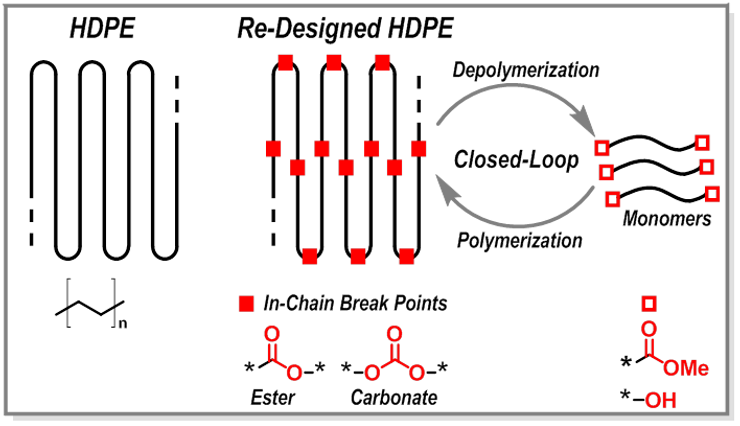
Prof. Stefan Mecking and his colleagues from University of Konstanz, Germany, have recently developed ‘polyethylene-like polymer’ containing ‘ester and carbonate break points’ – which allows chemical depolymerization of the polymer into its starting monomers. The recovered monomers can be repolymerized to form virgin-quality polymer, and the process can be repeated multiple times with full retention of material properties, forming a ‘Closed-Loop Life Cycle’ of Circular Economy. Their breakthrough is published in the journal ‘Nature’ [5].
The key innovation applied by the authors is the use of long-chain aliphatic (C18) building block, 1,18-octadecanedioic acid, which gives polyethylene-like polymer structure. It can be sourced from renewable palm oil/microalgae (via self-metathesis of oleic acid and then hydrogenation) and is commercially available. The authors were modified it (esterification & reduction) to install dimethyl-ester and hydroxyl end functional groups on the monomer (1,18-dimethyl octadecanedioate and 1,18-octadecane diol respectively, see Monomer Synthesis). Upon polycondensation of these monomers, 1,18-octadecane diol with 1,18-dimethyl octadecanedioate or 1,18-octadecane diol with diethyl carbonate under catalytic conditions, lead to form ester or carbonate in-chain functional groups – like connecting points for long aliphatic polyethylene-like chain, which also serve as ‘break points’ for the polymer (see PE-18,18 & PC-18).
