Research Highlight 5 – Circular Polydiketoenamines: The Journey so far.
- Sini Nalakathu Kolanadiyil
- Jun 13, 2022
- 13 min read
Polydiketoenamine (PDK) is a novel class of dynamic covalent polymer {also known as covalent adaptable network (CAN)}, and is synthesized via click-polycondensation reaction between β-triketone dimer and commercially available aliphatic triamine, tris(2-aminoethyl) amine (TREN). Polydiketoenamine is invented by Lawrence Berkeley National Laboratory, USA – Prof. Brett. A. Helms.
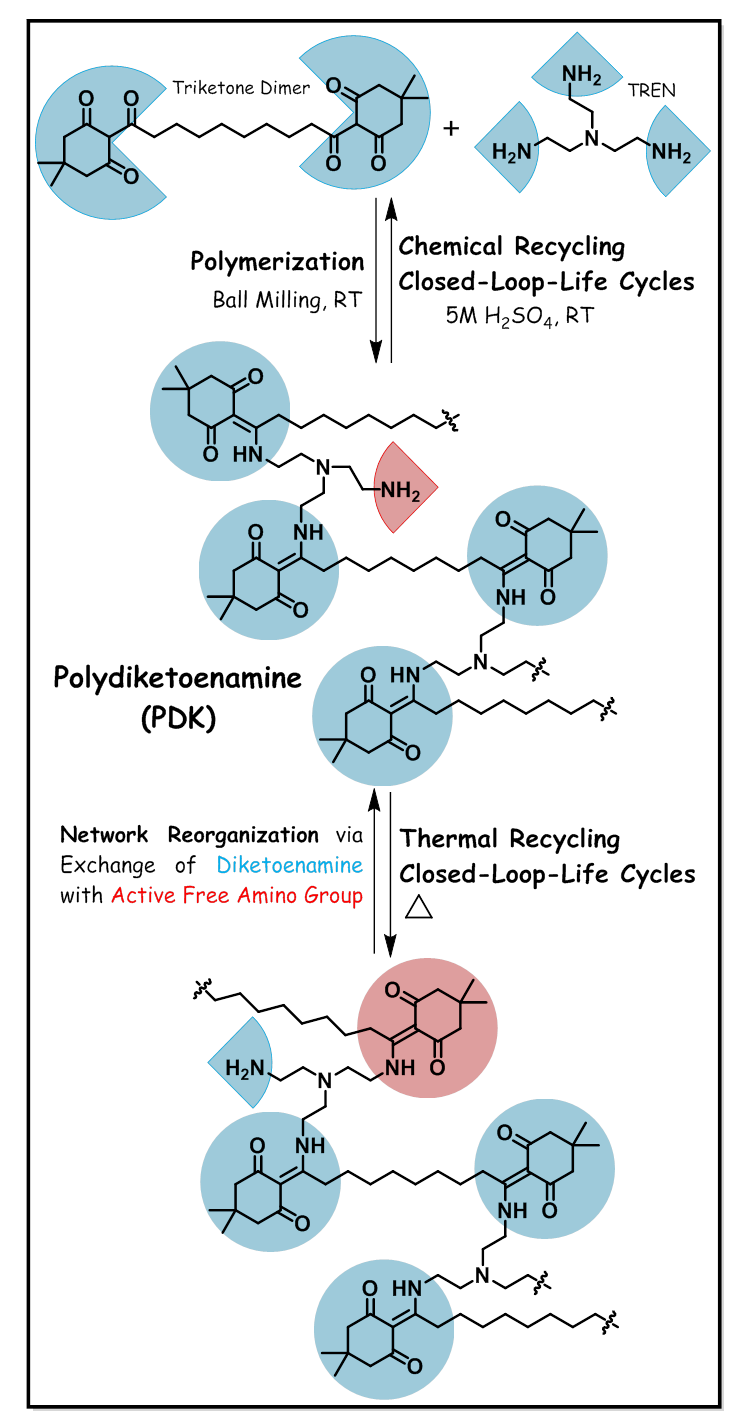
The first article of his discovery was appeared in 2019 in the journal “Nature Chemistry” [1]. In this article, Prof. Helms and team reported synthesis details and recycling (both by chemical and thermal means) of this novel circular polymer. The process for PDK synthesis is sustainable – simply by ball milling of the starting monomers (triketone dimer and triamine) for 45-60 minutes without the the use of any organic solvents (see Main Figure). Further processing of PDK resin, for example to produce samples with desired size and shape can be achieved by hot pressing ball-milled PDK powder at 150-200 °C. Tunability in thermal and mechanical properties was demonstrated in the article by designing polydiketoenamines using triketone dimers of varying aliphatic chain length, for example triketones based on adipic acid/dimedone, suberic acid/dimedone and sebacic acid/dimedone. The glass transition temperature (Tg) of resulting PDKs ranged from 100-120 °C. The main advantage of this novel PDK resin is that it can be chemically recycled infinite times, that is, depolymerization into its starting monomers via hydrolysis under acidic conditions and then repolymerization – fulfilling closed-loop-life cycles of circular economy (see Main Figure). In 5M aqueous sulfuric acid (H2SO4) solution, it only takes less than 12 hours at room temperature to completely depolymerize PDK resin and results in triketone monomer and ammonium salt – both of which can be easily separated in high purity (yield >90 %). The authors have mentioned in the article that 5M aqueous HCl (hydrochloric acid) is also equally effective for depolymerization. After separation, the crude triketone monomer was dissolved in potassium carbonate (K2CO3) solution and then re-acidified using HCl to precipitate pure monomer. Whereas the ammonium salt solution was passed through a reusable ion-exchange resin (amberlyst A-26 OH) to recover pure triamine monomer, TREN. Both recovered monomers, triketone dimer and triamine can be used in repolymerization to yield the same polymer with full property retention (virgin-like quality material and properties) or in different formulations to achieve different properties, for example, in combination with an aliphatic diamine such as poly(propylene glycol) bis(2-aminopropyl ether) or aromatic diamine such as 4,4’-oxydianiline to achieve storage modulus of 0.3-1.8 GPa. According to the authors, the reversibility of polydiketoenamine under acidic conditions was the 'breakthrough moment' in their discovery, which is opposite to the high hydrolytic stability of poly(ketoenamines) under acidic conditions. The second keto functionality in PDK backbone is responsible for this chemical degradability/recyclability which facilitated reversibility of enol-to-keto tautomerism {as opposed to poly(ketoenamines) in which enol-to-keto tautomerism is irreversible} [2,3]. PDK is stable in water and basic solutions {for example in 5M sodium hydroxide (NaOH)}. It has even shown long-term stability under mild acidic conditions, approximately for 1 month in 0.1 M aqueous H2SO4. In this case, PDK sample (rectangular bar) was found mostly intact, only color of the sample changed from brown to white due to partial hydrolysis on the surface. Thus, PDK’s acid degradability does not compromise its use in commercial applications – precautions need to be taken only where it comes in contact with strong acids (range: 0.5 M - 5 M H2SO4).
PDK resin can also be recycled only by applying heat because the diketoenamine bond can undergo exchange reaction with free amines available in the crosslinked network – which enables macroscopic flow and thereby thermal reprocessability – exhibiting vitrimer-like properties (see Main Figure). Traditional thermosetting resin cannot be recycled by applying heat/solvents due to its permanent covalently crosslinked three dimensional structure. Vitrimers are also permanently cross-linked networks [4], however due to the presence of dynamic bonds in the network, for example herein diketoenamines, they can undergo associative type exchange reaction (that is, exchange of a dynamic bond with an active free group through a short-lived intermediate) in the presence of heat stimuli, which allows network topology rearrangement and reprocessability. Here, the bonds are only broken after the formation of new ones (meaning no depolymerization), therefore vitrimers can maintain cross-link density throughout the exchange reaction (during thermal processing) and fully retain material properties after multiple reprocessing cycles – thus also solving problems associated with current industrial practice of mechanical recycling of traditional thermoplastic polymers (that is, polymer chain scission and thereby deterioration in material properties). For the above-mentioned reasons, vitrimers are considered as a sustainable alternative for both traditional thermosetting and thermoplastic polymers. However, most of the vitrimers cannot be depolymerized into its starting monomers, thus PDK vitrimer is a unique recyclable polymer for circulariry, that can be both chemically and thermally recycled to produce pristine-like quality material.
In the above-mentioned publication, the authors have demonstrated selective depolymerization of PDK and recovery of pure starting monomers from various real world scenarios. For example, recovery of monomers from mixed plastic waste stream containing PDK, polypropylene (PP) straws, polyethylene (PE) films, poly(ethylene terephthalate) (PET) bottle pieces, polyamide (PA) pellets, and polycarbonate (PC) based DVD parts – to mimic recovery from real world plastic waste. The monomer recovery was also possible from PDK compounded with various dyes (red, blue, yellow and black), carbon nanofiber and titanium dioxide. An important observation that is relevant for industrial recycling and worthy of mentioning here is that, when PDK resin depolymerizes, the triketone monomer precipitates out as white powder and the triamine monomer dissolves in 5M H2SO4. Thus, triketone monomer is filtered-off along with other acid insoluble plastic pieces, additives and pigments – most of them were insoluble except PA, which partially got dissolved in 5M H2SO4. The authors have mentioned that the dissolved PA can be removed from triamine containing H2SO4 solution by adding water, which precipitates PA (and triamine salt is soluble in water), thus easily separable. The triketone monomer was recovered by extracting it from these filtered plastic pieces/additives/pigments using potassium carbonate solution (here only solubilization of triketone occurs), followed by precipitation in HCl. PDK resin is also suitable for fibre-reinforced plastic (FRP) manufacturing, for example in aerospace industry. Chemical recyclability of PDK makes possible for FRP recycling – the recovery of triketone, fibreglass cloth, and flame-retardant from a PDK based fibre-reinforced composite is also demonstrated in the article – all of these can be re-used – thereby ‘closing the loop'.
In their second research article on PDK published in “Angewandte Chemie” Prof. Helm and group focused on establishing relationship between incorporation of flexible or rigid units into PDK backbone (that is, conformational degree of freedom in the network) on its thermal, mechanical and rheological properties [5]. For example, they have used diamine such as isophorone diamine (IPDA) and trimethyl hexamethylene diamine (TMHDA) to incorporate rigid and flexible units respectively during PDK synthesis along with triketone (based on sebacic acid/dimedone) and TREN at different molar ratios (20-60 %). As the authors anticipated, the incorporation of rigid units increased Tg of PDK resin (122-138 °C) whereas flexible units decreased it’s Tg (100-85 °C) – with increased amount of diamine content. The observed linear relationship with Tg also indicated that these diamine units are homogeneously distributed in the PDK network. PDKs containing IPDA/TMHDA units exhibited storage modulus (E’) of 1.4-2 GPa and tensile strength of 18.5-30 MPa at ambient temperature. The authors have stated that these values are similar to epoxies, nylon-6 and polyurethanes, thus they hope that PDKs can be a potential replacement for these polymers in various industries, especially for non-recyclable PU in automotive industry (tensile strength of commercial PU rubbers – 0.6-44.1 MPa). The molecular weight of polymer chains between crosslinks for flexible PDK was in the range of 3.8-9.6 kg/mol and for rigid PDK it was in the range of 4.3-11.9 kg/mol. The authors have found that both the molecular weight (MW) of polymer chains between crosslinks and conformational degree of freedom in that polymer chains (flexibility/rigidity) had impact on its rheological (processing) properties. The increased amount of flexible diamine content in PDK decreased the stress-relaxation time whereas rigid diamine content resulted in opposite results. For example, flexible PDK with 6.3 kg/mol MW (40% TMHDA diamine content) showed a stress-relaxation time of 110 seconds at 150 °C whereas rigid PDK with 7.8 kg/mol MW (40% IPDA diamine content) showed higher stress-relaxation time of 450 seconds at 150 °C. This is because flexible units (meaning higher conformational freedom) allow easy diffusion of reactive groups which in turn enables faster bond exchange reaction and easy flow. This is also reflected in the activation energy (Ea) required for dynamic bond exchange reaction, flexible PDK showed low Ea of 47-43 kJ/mol as compared to rigid PDK which exhibited Ea of 54-62 kJ/mol.
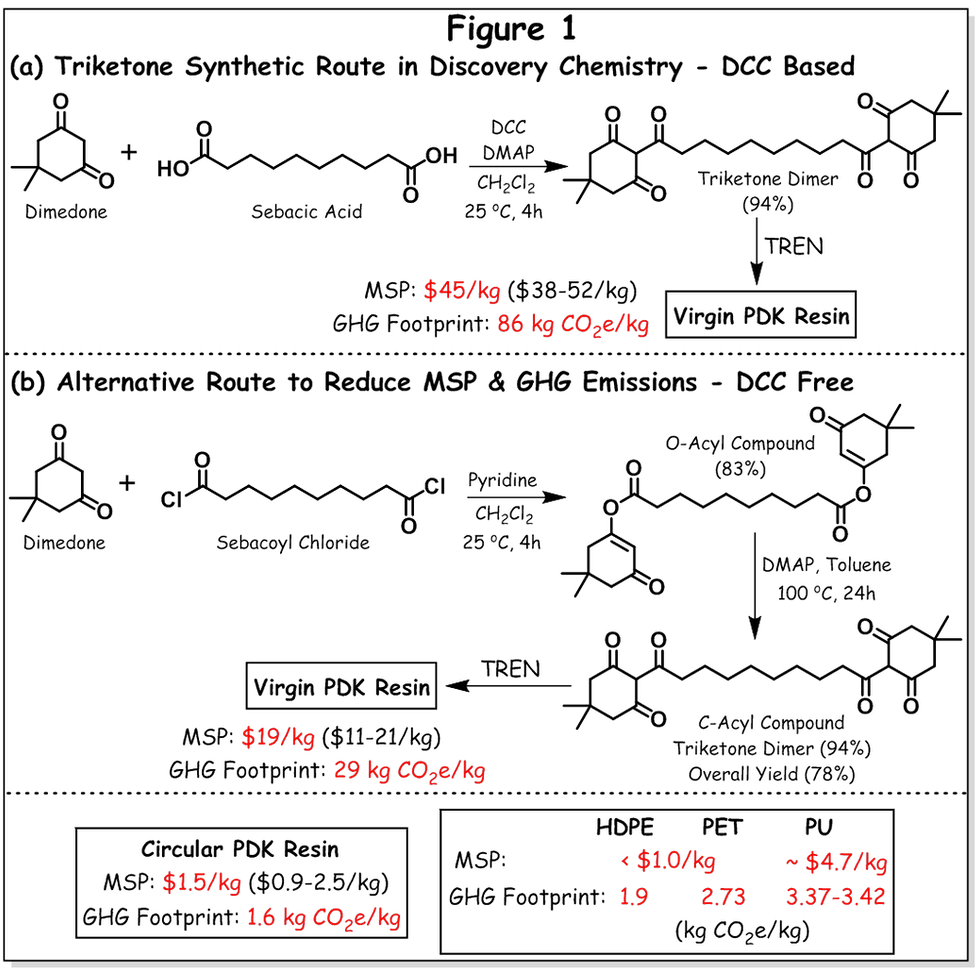
Next, Prof. Helm and group turned their focus on bringing this novel circular PDK resin into the market. For that, they have conducted techno-economic analysis and life-cycle assessment (cradle–to–facility gate) of PDK, which is published in “Science Advances” [6]. In this article, they have estimated minimum selling price (MSP) and greenhouse gas emissions (GHG footprint) by modeling three different scenarios for PDK production. The first plant is based on primary PDK resin – that is only for virgin resin production of 20,000 metric tons (MT) annually. The second plant is based on circular PDK resin – that is, the plant facility only for chemical recycling of post-consumer PDK waste into its starting monomers – triketone and TREN, and then repolymerization by utilizing these recovered monomers to produce pristine-quality PDK. The third plant is for mixed PDK resin production, which consists of both circular PDK resin and primary PDK resin. Here, primary PDK resin will be added to make-up a total of 20,000 MT annual production. The authors envision that in the initial commercialization stage, post-consumer PDK waste recovery from ‘product take-back scheme’ at smaller scale would be more feasible than from municipal waste stream, since PDK production should be much larger volume than mentioned here to collect it from US municipal waste stream. The authors estimated MSP for virgin PDK resin is $45/kg and for circular PDK (recycled PDK) is $1.5/kg (see Figure 1, in brackets optimistic to pessimistic case is provided). The major contribution to the high cost of virgin PDK came from material cost (~75% of total MSP) for its production and the rest is accounted for waste management cost (22%), operating cost and capital cost (~2%). The material cost required for the synthesis of triketone monomer – one of the starting precursors of PDK synthesis – is very high (~ 49% of total MSP). This is mainly due to the catalyst used, that is the cost of the production of DCC (N,N’-dicyclohexyl carbodiimide) catalyst ($15-20/kg) – which also produces hazardous waste such as N,N'-dicyclohexylurea (an immunosensitizer) – thereby also contributing to the waste management cost. The other cost contributors are DMAP catalyst {4-(dimethylamino)pyridine} and DCM solvent (dichloromethane) used for triketone synthesis. These also contributed to high GHG footprint of virgin PDK, which is 86 kg of CO2 equivalent per kilogram of product. That is, 48% of GHG footprint came from cyclohexylamine, pyridine and chlorosulfonic acid – chemicals used for DCC synthesis, 9% from DMAP and 6% from waste management. The contribution of the other main precursor for PDK production, that is triamine TREN was 9% to the total MSP (~$20/kg) and 7% to the total GHG emissions.
The low cost of circular PDK resin is mainly because the depolymerization of PDK resin to recover triketone and TREN (the major two precursors for PDK resin production) only requires low cost and less hazardous reagents such as H2SO4 (for chemical depolymerization), K2CO3 and HCl (for triketone extraction and re-acidification), NaOH (for ion-exchange process of TREN). The major cost contribution of circular PDK accounted for capital cost (23% of total MSP) and acquisition of clean waste stream (36% of total MSP). The GHG footprint of circular PDK was only 1.6 kg of CO2 equivalent per kilogram, which came from the use of NaOH in ion-exchange process for the recovery of TREN (20%, ~1.4-2.7 kg of CO2 equivalent per kilogram of NaOH), natural gas combustion (36%) and transportation (from sorting/collection facility/deposit centers to the plant).
The circular PDK showed competitive performance in comparison to polymers currently used in packaging {high density polyethylene (HDPE) – 1.9 kg CO2e/kg of resin and poly(ethylene terephthalate) (PET) – 2.73 kg CO2e/kg of resin} and consumer {polyurethane (PU) – 3.37-3.42 kg CO2e/kg of resin} products in the market in terms of GHG footprint. The MSP of circular PDK was little higher than HDPE and PET (<$1/kg), but much less than PU (~$4.7/kg) (see Figure 1). However, on the contrary, the virgin PDK and mixed PDK with high waste recovery rate of 44-100% (modeled in Plant 3) exhibited high cost and GHG footprint. The authors think that mixed PDK resin would be a more realistic scenario, thus it is important to reduce the cost and GHG footprint of virgin PDK. Hence, they targeted to find alternative synthetic procedure for triketone synthesis in the discovery chemistry.
Prof. Helm and group next turned their focus in this direction – in search for an alternative DCC-free triketone synthetic procedure. This work is recently published in “ACS Sustainable Chemistry & Engineering” [7]. In the alternative chemistry, the authors have replaced sebacic acid with sebacoyl chloride in an attempt to explore a DCC-free route, but also to prevent the usage of large amount of DMAP catalyst – since these were the major contributors to the MSP and GHG footprint. According to the authors, the reaction of 1,3-diketone (or dimedone) with sebacoyl chloride should yield triketone directly via rapid rearrangement of O-acyl compound to C-acyl in the presence of a suitable catalyst (for example in DMAP). However, as opposed to their expectation, in the initial screening, the authors have found that the rearrangement reaction was suppressed in DMAP due to the presence of acidic by-products. At the same time, the use of catalysts such as pyridine or samarium (III) chloride (SmCl3) only yielded O-acyl product in quantitative manner. Thus, the authors decided to conduct triketone synthesis in step-wise (see Figure 1), at first O-acyl compound was synthesized by reacting dimedone with sebacoyl chloride in the presence of pyridine in DCM at 25 °C for 4 hours. Then, the O-acyl compound was purified by removing by-products via aqueous extraction, followed by recrystallization from ethyl acetate. In the second step, rearrangement of O-acyl to C-acyl was performed using only catalytic amount of DMAP (as opposed to discovery chemistry in which superstoichiometric quantity was used) in toluene at 100 °C for 24 hours. Techno-economic analysis and life-cycle assessment revealed reduction in both MSP and GHG footprint. The MSP of virgin PDK produced via alternative chemistry (DCC-free route) is $19/kg and GHG footprint is 29 kg CO2e/kg – that is, 57% reduction in MSP and 66% reduction in GHG footprint as compared to discovery chemistry based virgin PDK (DCC based). The authors have stated in the article that the major contribution to the MSP and GHG footprint in the updated procedure came from dimedone (starting monomer for triketone synthesis) and TREN (triamine precursor for PDK synthesis), and in future studies the authors hope to replace them with bio-based counterparts to reduce the cost and fossil carbon content of virgin PDK.
What’s next in-store for PDK? Well, very recently, Prof. Helm and group innovated towards achieving temperature tunability in chemical recycling of PDK. This work is published as a preprint in “ChemRxiv” [8]. They have varied number, type and placement of heteroatoms (oxygen or nitrogen) with respect to the keto functionality in triketone ring to produce PDK resin with varying temperature acid degradability (see Figure 2). The triketone starting monomer in the discovery phase chemistry was produced from dimedone and sebacic acid (PDK1). Herein, in the exploration phase chemistry, the authors have introduced three more different triketones based on (i) dihydro-6,6-dimethyl2H-pyran-2,4[3H]-dione and sebacic acid (PDK2), which contains O atom near to one of the keto groups on the backbone, (ii) meldrum’s acid and sebacoyl chloride (PDK3), which contains O atoms near to both keto functionality, and (iii) dimethylbarbituric acid and sebacoyl chloride (PDK4), which contains an additional keto functionality and N atoms near to all keto groups. PDKs produced from these triketones exhibited Tg in the range of 96-136 °C and storage modulus of 1.8-2.1 GPa in the glassy region and 5.3-6.9 MPa in the rubbery region. These PDKs showed acid degradability in 5M HCl at varying temperatures – at 0 °C for PDK1, 20 °C for PDK2, 40 °C for PDK3 and 60 °C for PDK4. Thus, blends and multi-layer packaging material made from these PDKs can be selectively depolymerized to recover corresponding triketones (& TREN) by simply changing the temperature under acidic conditions. Chemical recycling of all PDKs showed good recovery of triketones (88-99% recovery), except PDK3 (51% recovery) in which chemical recycling resulted in side product formation, β-keto acid.
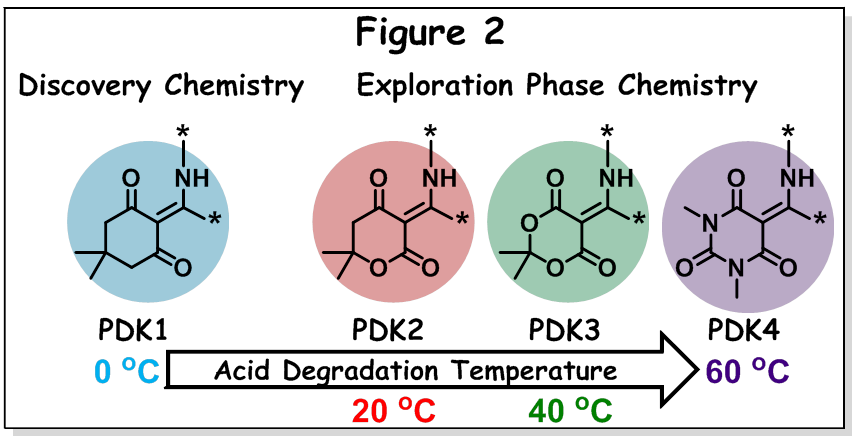